What we do
Our passionate and experienced people deliver successful clean energy projects globally.
Technologies
Driving a clean energy future through state-of-the-art renewable technologies.
See all technologiesResources
Browse our latest resources, including company updates, customer stories, industry insights, and research reports.
See all resourcesCareers
Join a collaborative team of passionate individuals who engage in meaningful, stimulating, and world-changing work.
Learn moreAbout RES
We live our mission, celebrate the people making it happen and transform the way the world produces and consumes energy.
See about usOur offices
Like our business, we’re truly global – but proudly local. Find contact and location details for every RES office.
Contact us-
Home
/
Resources
/
Case Studies
/
Harnessing the value of independent condition monitoring services
Harnessing the value of independent condition monitoring services
by RES | Jan 25, 2024 | Reading time: 2 min
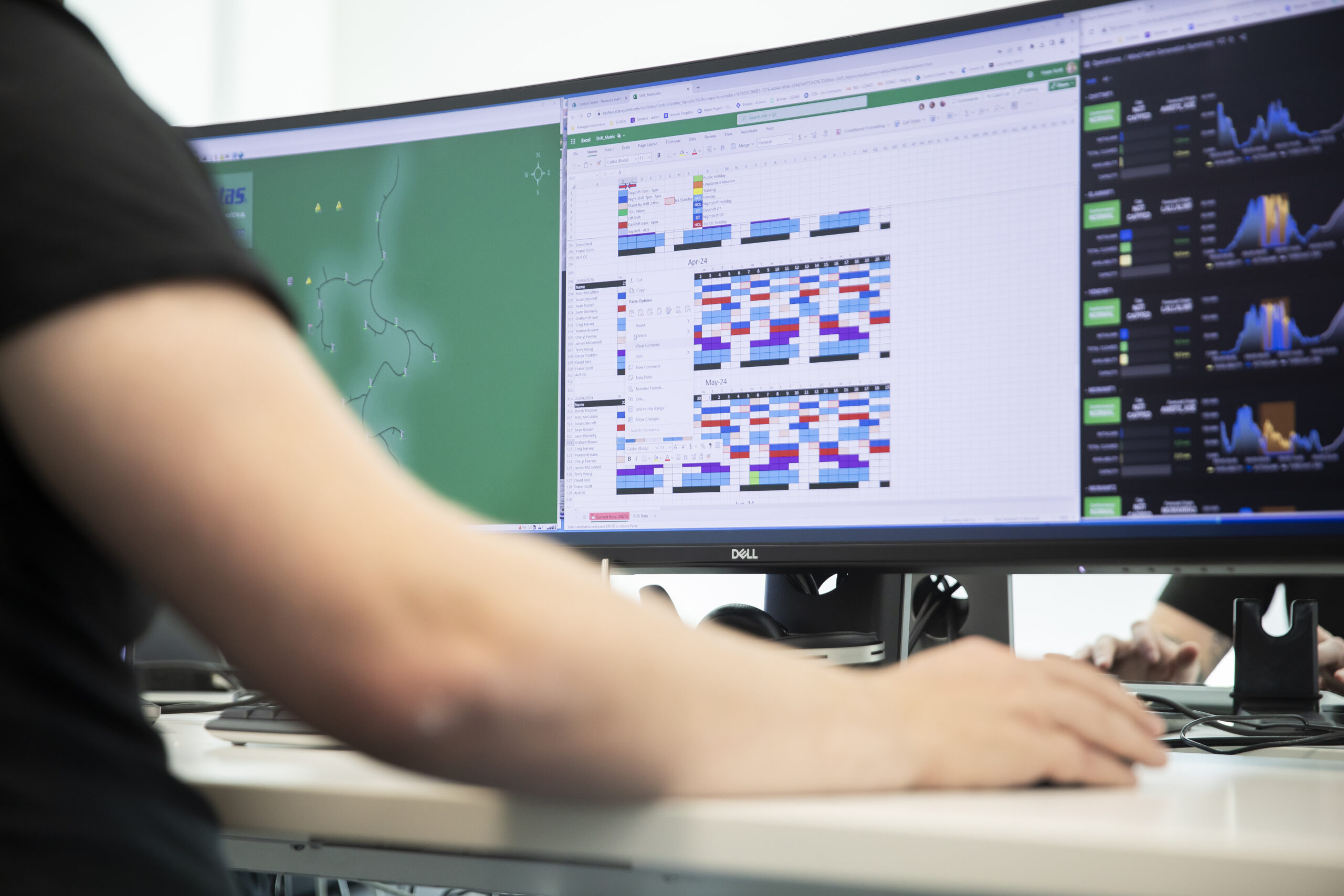
Condition Monitoring Systems (CMS) are used by original equipment manufacturers (OEMs) to manage defect and availability warranty obligations. Whilst this information provides benefits for asset managers and owners it isn’t often detailed enough for them to gain a holistic view of the health of assets, which is where independent condition monitoring services step in. Independent condition monitoring services are customary practice within technical asset management to help validate the data obtained from the OEM as well as provide the asset owner confidence in the asset’s health.
At RES, we use wind turbine drivetrain data, typically vibrational and oil data, which is taken from the CMS system and combined with other data types, such as SCADA data. This data allows our engineers to gather a full picture of asset health, enabling short term and strategic longer-term maintenance decisions to be made. For instance, we can identify anomalies that otherwise may not be picked up, preventing major component failure.
The works
As part of the independent condition monitoring service which we provide for a wind farm in the UK, we conduct independent analysis of the vibration and oil data produced by the OEM. Using this analysis, the team remotely identified a gearbox plant failure. The OEM didn’t initially agree with the RES prognosis; however, our team knew that with the damage already suspected in the gearbox, the condition of the gearbox would become worse if left unaddressed.
We highlighted our findings to both the asset owner and OEM with a recommendation to inspect the gearbox within a short timeframe to prevent any further damage. The warranty and obligation period with the OEM was due to shortly expire, therefore we wanted to ensure that the matter was resolved promptly so that the asset owner wasn’t liable for any further failures.
Whilst the inspection was arranged, the turbine continued to run whilst we monitored the fault, avoiding additional downtime. Independent CMS can be utilised in forecasting potential faults and managing targeted proactive and preventative long and short maintenance.
An endoscopic inspection of the gearbox was arranged which found extensive damage including material degradation, micropitting to tooth tips and indentations marks on the Planetary Stage Bearing, which we had predicted as likely. Following the investigation, a recommended action for the gearbox to be replaced was made “at the earliest opportunity to prevent catastrophic failure”.
Results
A gearbox replacement can cost up to £500K but thanks to our independent CMS, the issue was identified, and gearbox replaced within the warranty period, avoiding a catastrophic gearbox failure. Early identification of the issue saved our customer a vast amount of expense, downtime, and loss of yield production due to the size and type of the main component as well as the potentially costly, lengthy and unpredictable access to the offshore location.
